Who's Got Your Back?
Increase plant productivity, avert asset failures and minimize downtime. Motornostix® is the industry-standard solution for shredder monitoring. With full-service and cost-effective shredder health and performance management, we monitor our customers' equipment 24x7. Who's got your back?
Do More With Less
Staffing challenges, changing industry economics and supply chain constraints require that you do more with less. Sometimes with a lot less. And without compromising the health of your critical plant assets. Motornostix® is there to help you keep your finger on the pulse of your operation.
Piece Of Mind
We are the missing piece in your plant health and performance management. Quietly running behind the scenes and telling you what you need to know, when you need to know it. So you can focus on running your business and staying ahead of the game. Motornostix®, your peace of mind.
About Us
For more than twenty years we have been on a mission to maximize shredder performance while caring for asset health. Our customers rate amongst the best performing plants for their mill size in the industry. Continuous monitoring of your plant assets helps identify opportunities for improvement and predictive care that has resulted in many early-warnings to our customers over the years, preventing failures and protecting and extending the life of their valuable plant assets.
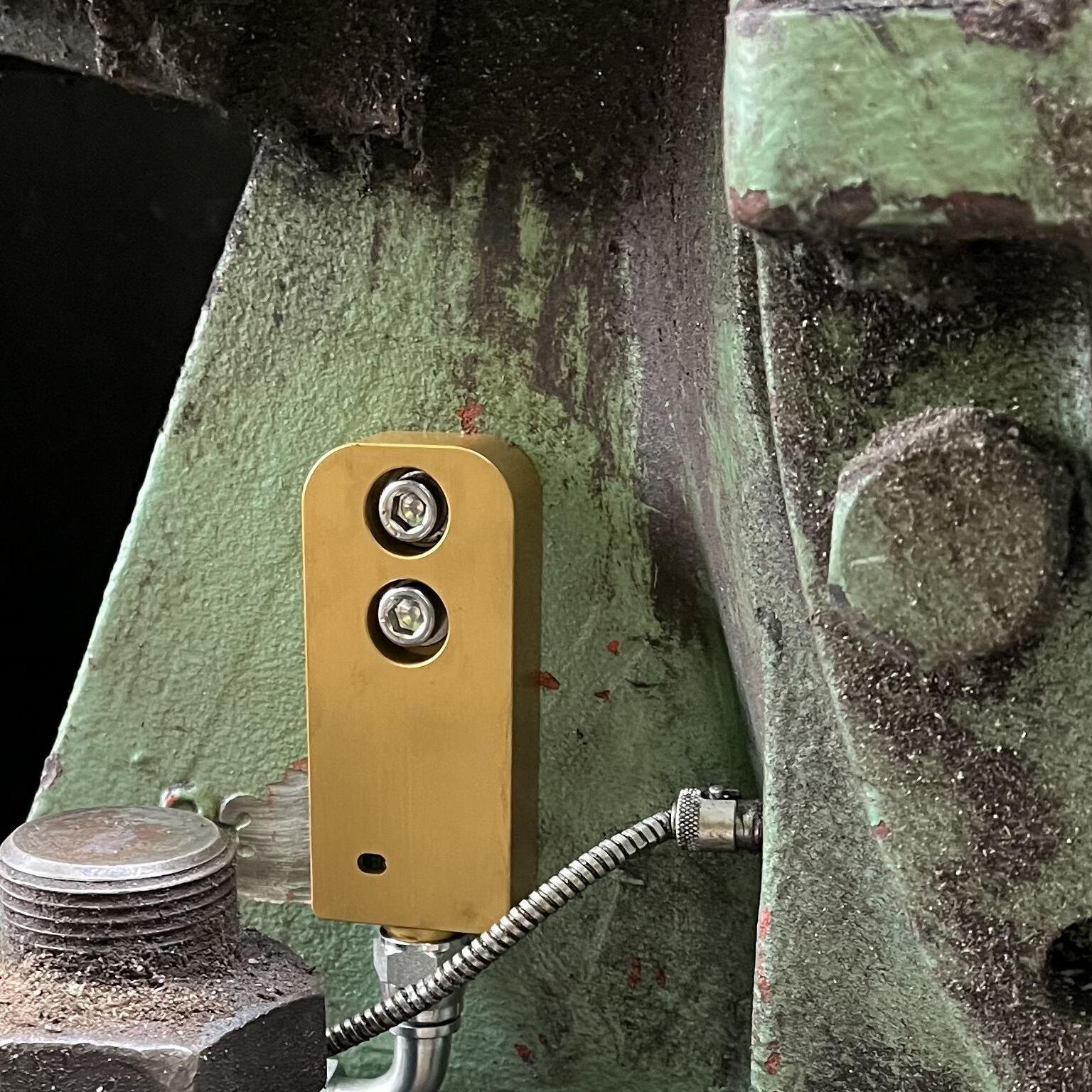
Our Mission
We provide best-in-class shredder health and performance monitoring equipment and services and leverage our extensive industry experience in support of our customers.
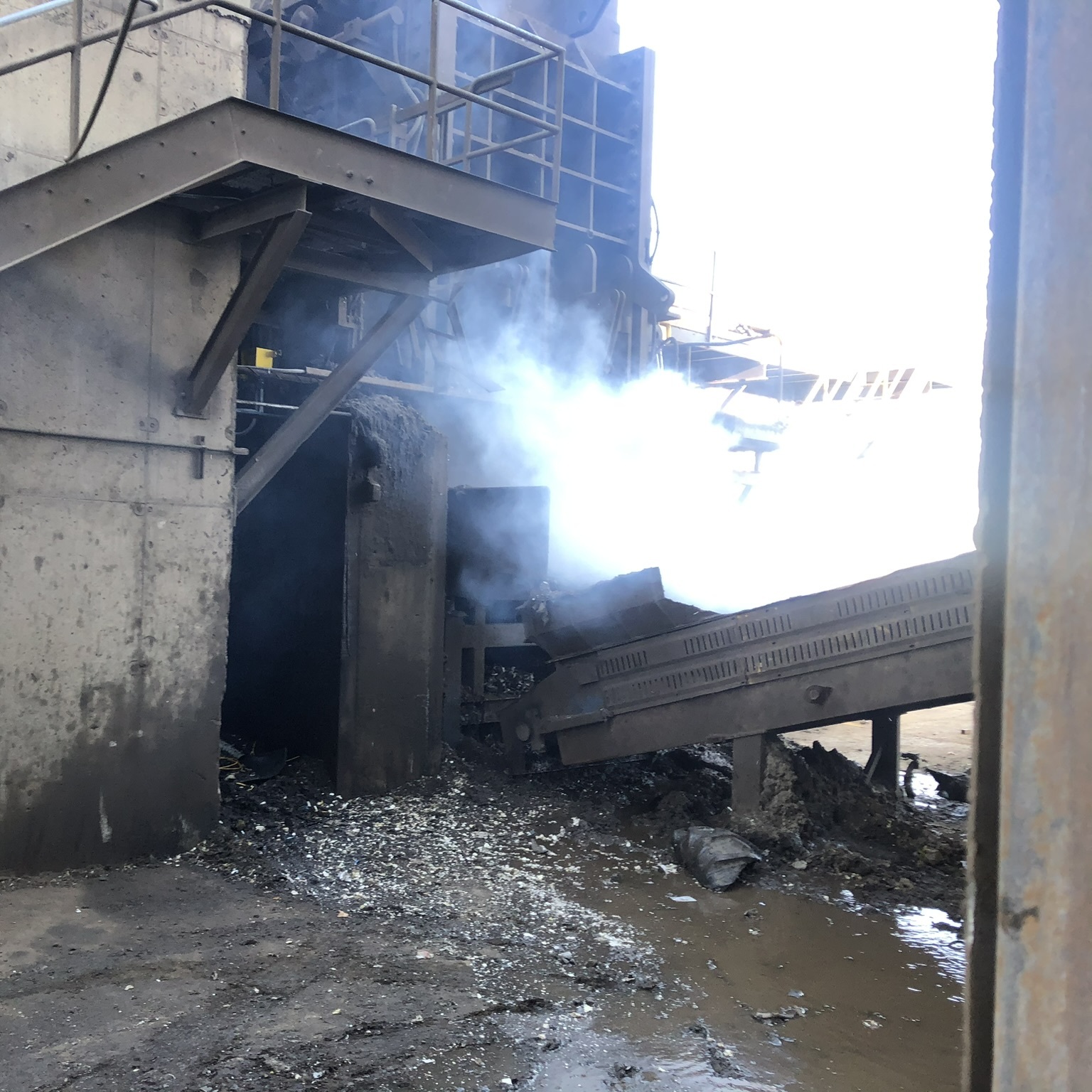
Our Plan
We partner with you and your team using our tools and technologies to continuously measure, improve and refine shredder performance while maximizing asset health.
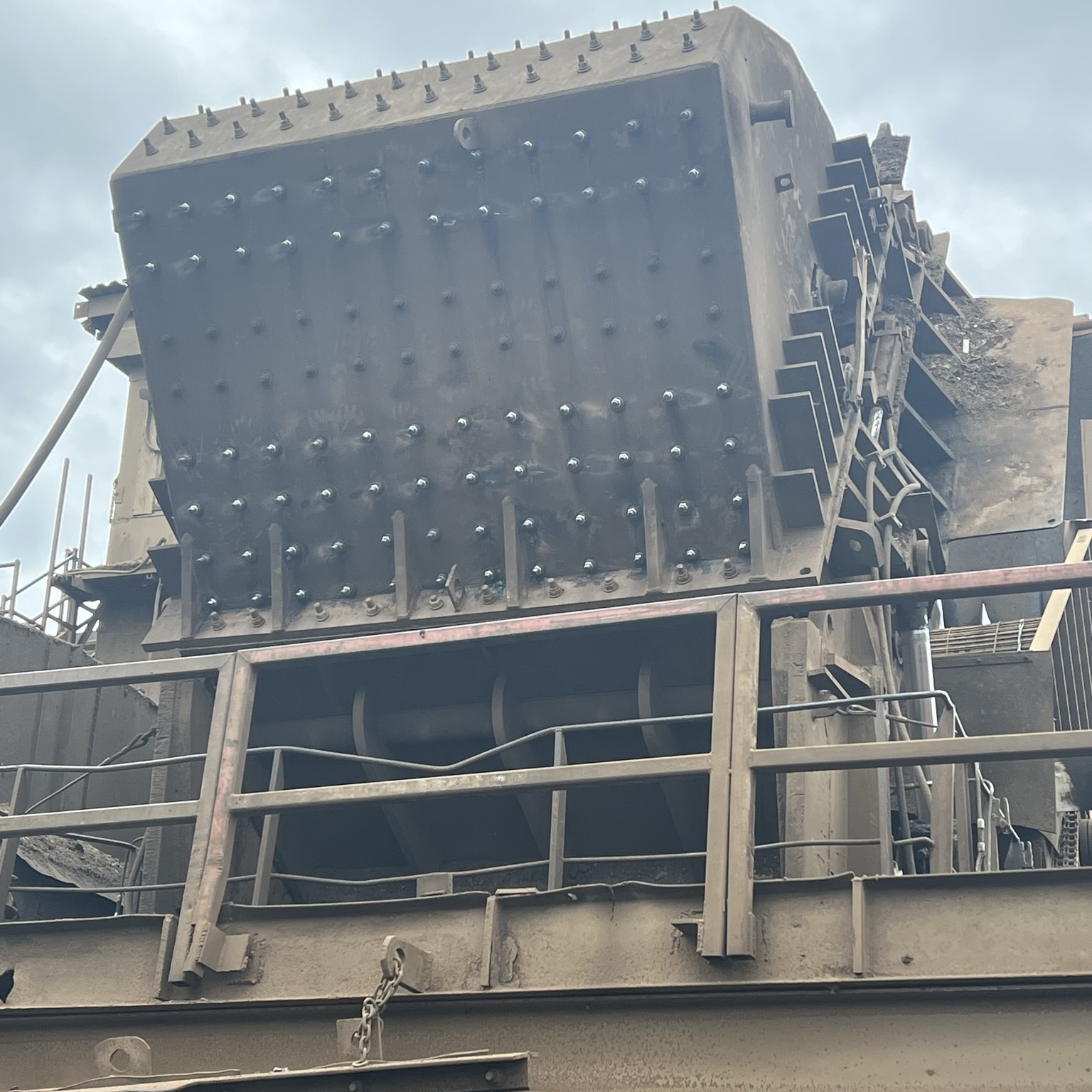
Our Vision
Your shredder plant, highly profitable and astonishingly productive with wonderful asset health and safety resulting from predictive maintenance practices.
Services
Knowing when to run equipment and when to repair equipment can mean the difference between safe operation with long equipment life versus less desirable alternatives such as unplanned downtime and catastrophic failures. Skilled operators often feel or sense equipment issues but have no way to know if their sensations are correct or to communicate their sensations to management. Motornostix® sensors are connected directly to the shredder and to the drive motor[s], looking at three axes of bearing data, and can sense issues reliably to aid in problem detection and identification. We also contribute to efficient plant operation by monitoring values such as power consumption and output, offering reports on these items to improve daily throughput.
Data Safety and Access
• We store your data in a Tier-3 facility so it is safe, secure
and accessible.
• It is accessible via any device that can connect to the
Internet and run a browser.
• We have resolved a number of issues over the years by
providing vendors access to customer data for troubleshooting
purposes. This has reduced the lead time to resolution, greatly
assisted with root cause analysis and limited the cost involved
since often times no vendor visits were required. This has been
particularly helpful with vendors who are not state-side, like
Alstom, Actom and WEG.
Alarms
• From the monitored data, Motornostix® provides
alerts, alarms and information to protect the health and safety
of personnel, equipment and the environment around metal
shredders.
• All key measurables both from our sensors and the Multilin are
collected, measured and monitored in real-time. Alarms are
raised to notify you of developing health conditions during your
production run. These can be anything from surfacing flaky RTDs
(e.g. damaged, over-temperature or loose terminal connections)
to vibration alarms indicating damaging vibration impacting
machine health.
Analysis
• Automatically mining data on the backend.
• Tools for analysis if needed.
• Analysis if needed.
• Expertise if needed.
• The Motornostix® system captures vibration
waveforms (think bearing MRI or X-Ray) on each bearing in all 3
axes (axial, horizontal & vertical) and deconstructs these
comprehensive measurements into their components parts (e.g.
comparing synchronous vs non-synchronous energy as a basic
example) to evaluate bearing health over time. Waveforms are
captured at idle on every run day, thus forming a comprehensive
picture of machine health over time. And all of this information
is available via our portal to you, and your vendors as
permitted.
Monitoring
• All your shredder health and performance data is streamed to
our Tier-3 Data Center where it is available to you 24x7.
• We keep ALL your history online. Want to compare last month to
this month? It’s online. So is last year and the year before
going all the way back. This is a really powerful feature of our
system typically not provided by process control systems at
recycling plants.
• This is one of the main reasons that our large corporate
customers really like our system, since ALL the data for ALL the
plants is available ALL the time at your fingertips.
Reporting
• We provide you with two daily reports for each site – the
performance
report
covers exactly that – how well did the site perform against
expectations for the last 24h window (defined by you)? This
information includes runtime, idle time, motor utilization,
thermal capacity, production output and electrical efficiency.
• The
health report
details machine health metrics to answer the question – what was
the impact on machine health for the performance achieved? The
health report also surfaces developing machine health
conditions. The report shows vibration data across the drive
train in an easily-consumable format so you can compare
day-on-day and investigate and identify associated root causes.
• Motornostix® provides notifications of significant
events.
• Motornostix® provides reports of critical
performance.
• Motornostix® provides tools for monitoring and
analysis.
• Motornostix® provides protection against unplanned
downtime.
• Motornostix® provides protection against
catastrophic failures.
System Reliability
• Industry standards for operation and security.
• The only potential damage to our system generally occurs out
at the mill.
• Our mill sensor and cables are armored and jacketed with an
aerospace thermal fire-sleeve along with a stainless steel woven
braid. This design has proved pretty impervious even to the
destructive nature of the shredding process, but occasionally
damage, either thermal (e.g. mill fire) and mechanical (e.g. car
falls from in-feed chute onto our sensor) occurs.
• Any such damage would require sensor/cable replacement at your
cost.
• If a sensor fails without any observable damage, then we offer
forward replacement of the part at our cost.
• Whilst it varies from site to site, mill sensor lifetime is
often measured in years.
• If some other component of our system fails (e.g. a computer)
without overt damage, then we cover the cost of the replacement
item.
Installation
• The installation cost includes all the Motornostix®
specific equipment to be installed at each site including cabinets,
power systems, computer equipment, cables and sensors.
• Our system comes pre-assembled (think Legos) to ease installation
and minimize downtime.
• We generally need some help from your site electrical contractor
to provide power to our cabinet, running conduit if required, and to
assist with welding our junction boxes out at the mill.
• An installation takes approx. 2-3 days depending on existing site
infrastructure, and most installations typically take place over a
weekend to minimize plant downtime.
Facts
Our commitment to our customers success is evidenced by our longevity in this industry.
Continuous
Monitoring
Hours
Data
Points
Collected
Hours Of Support
Hours of
Experience
Known by the companies we keep
Contact Us
Please contact us for more information. We love to hear from customers and potential customers alike.
Address
P.O.Box 498136Cincinnati, Ohio 45249, USA
Phone Number
513-334-3550
sales@motornostixusa.com